Before settling on engineering as a career path, I dabbled in semi-professional 2D animation, graphic design and video production. Those interests have never left, but engineering, or more specifically electro-mechanical engineering and product development, are part of my identity. Here are a few highlights:
– Present – 2022 –
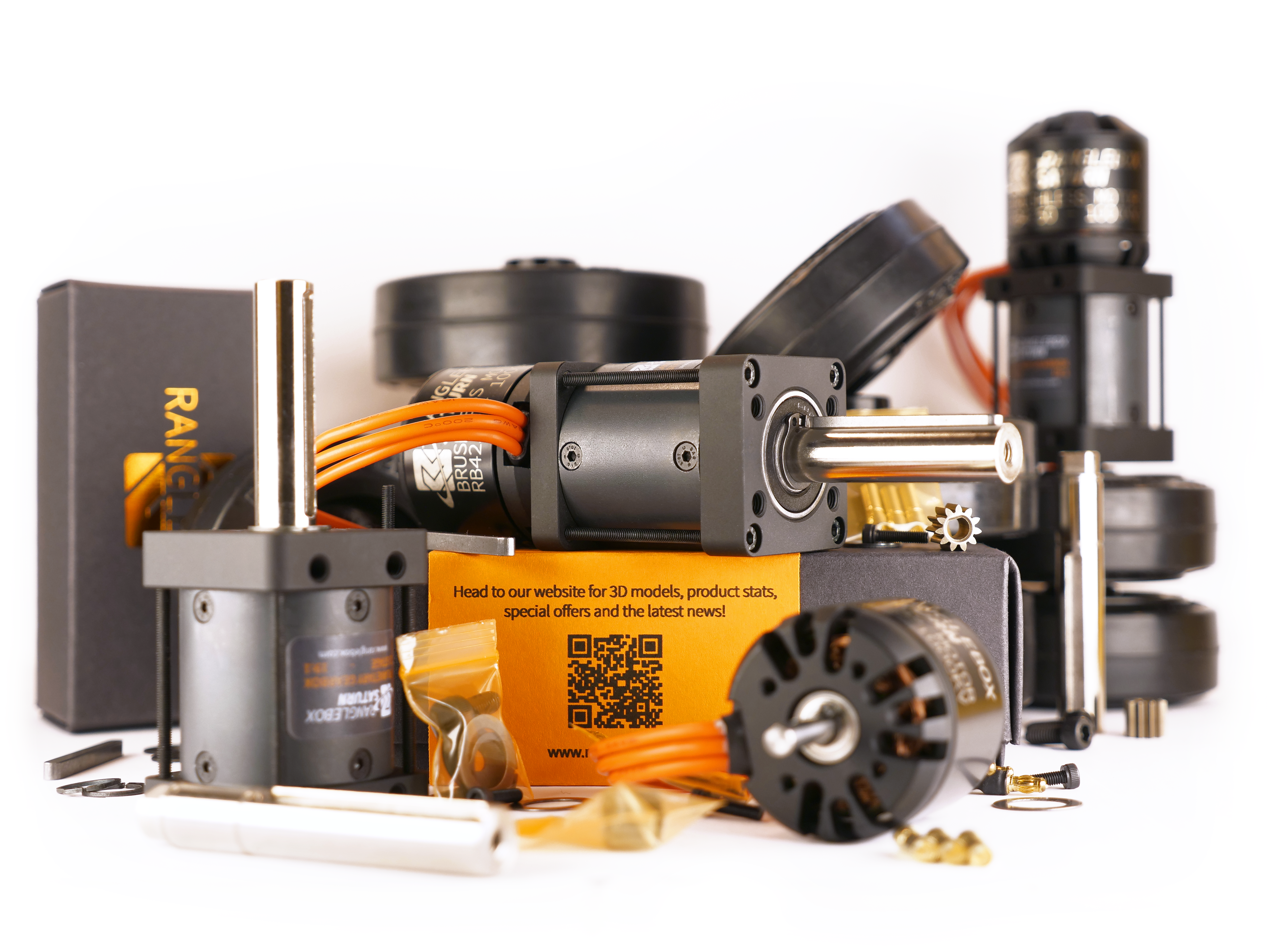
In 2022 I decided to make several life changes at once by moving to Sheffield and “going solo”. Solo means leaning into Ranglebox Ltd, my own venture, and working on dozens of small product ideas previously doomed to the backburner.
Originally born out of a frustration for the lack of high quality, cheap, purpose-made products in the robotics space, I now have multiple motor, gearbox, controller and hardware lines. Ranglebox products feature at virtually all combat-robotics competitions around the world in my fellow enthusiast’s machines!
I have also taken on multiple engineering clients as a contractor, providing SOLIDWORKS firepower and expertise for tech start-ups. I have worked on the big, the small, the delicate, the heavy-duty, the slick and the slightly repetitive. A journey!
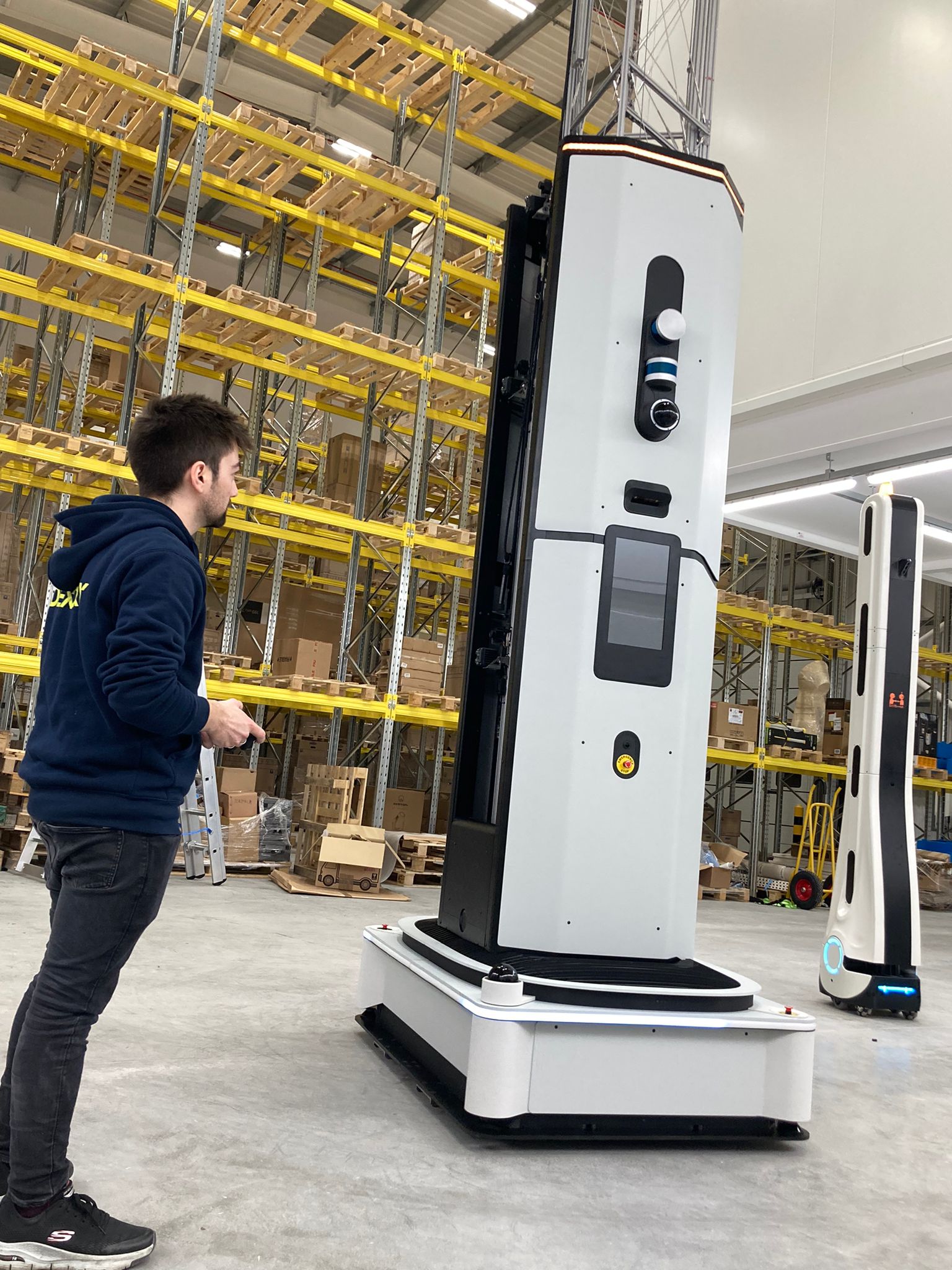
A highlight of my time as an independent engineer has been working with Dexory. They have developed a world-leading warehouse management system, and at its centre is a 400KG, 12m+ tall, fully autonomous telescopic robotic platform which is packed with tech.
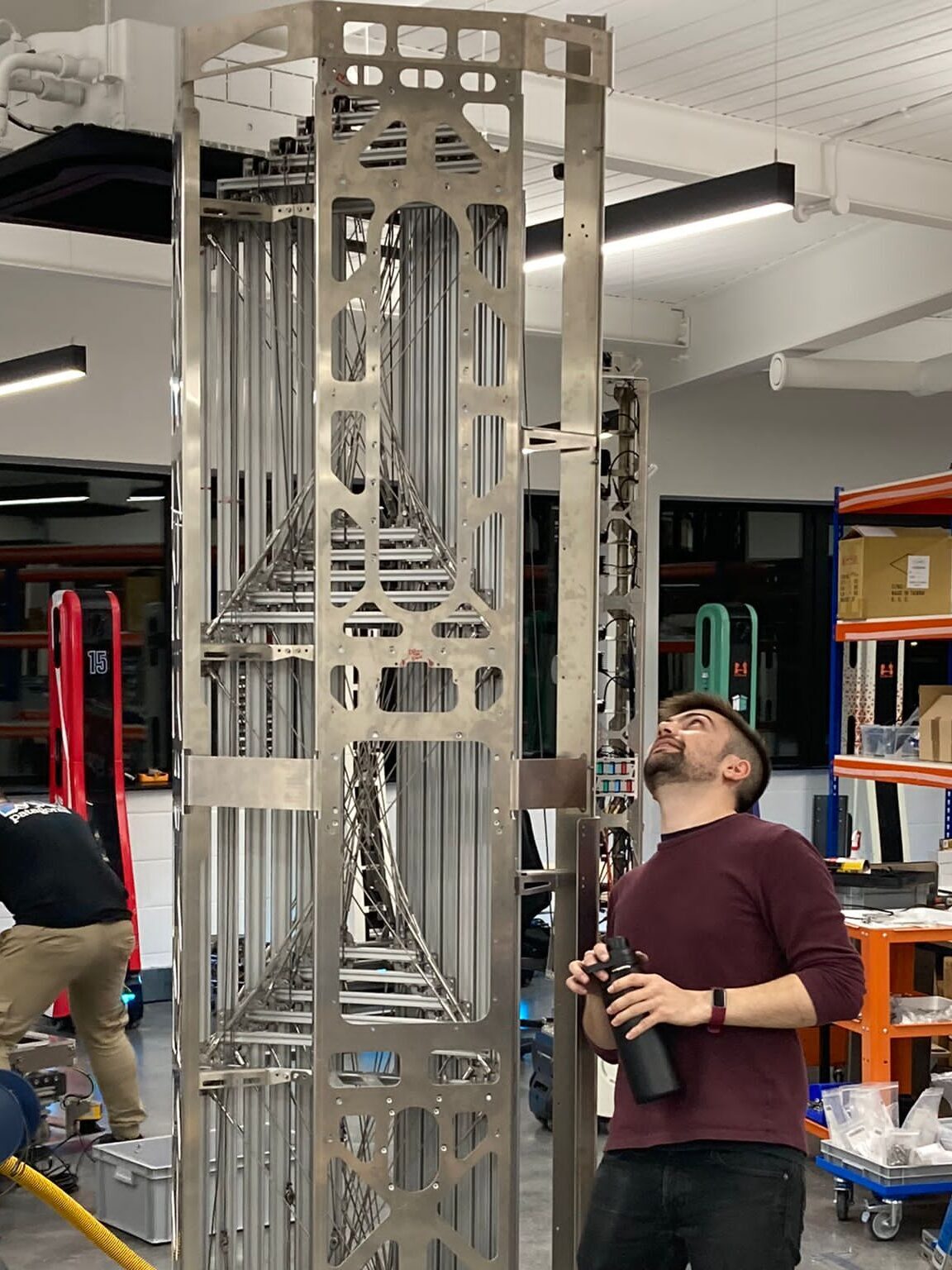
I was commissioned by Dexory to help them kick off the creation of this huge machine. I worked closely with their then-small (now huge!) team of hardware engineers to pump out a first prototype build in a matter of months. I took on a majority slice of the SOLIDWORKS heavy lifting, regularly travelled to their spaces, and used all of my experience to quickly develop mechanical systems and stare-down some seriously big engineering challenges.
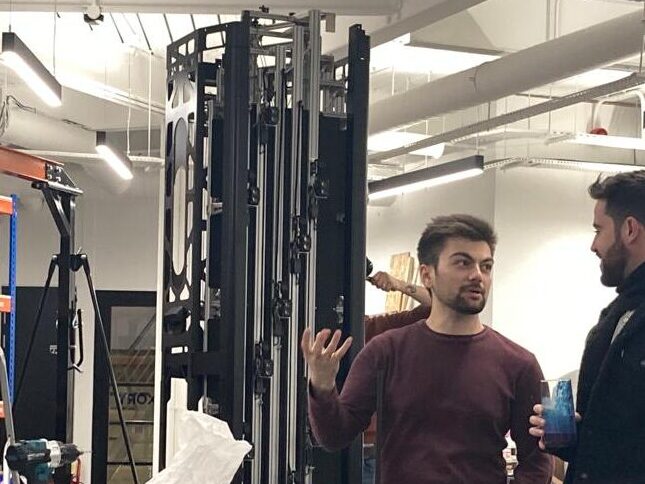
A significant part of the present-day product carries my design DNA, both externally and internally. Whether it’s 3D printing, CNC, sheet metal, drivetrains, cable management, or any other electro-mech design or manufacturing discipline, this had it!
– 2022 – 2021 –
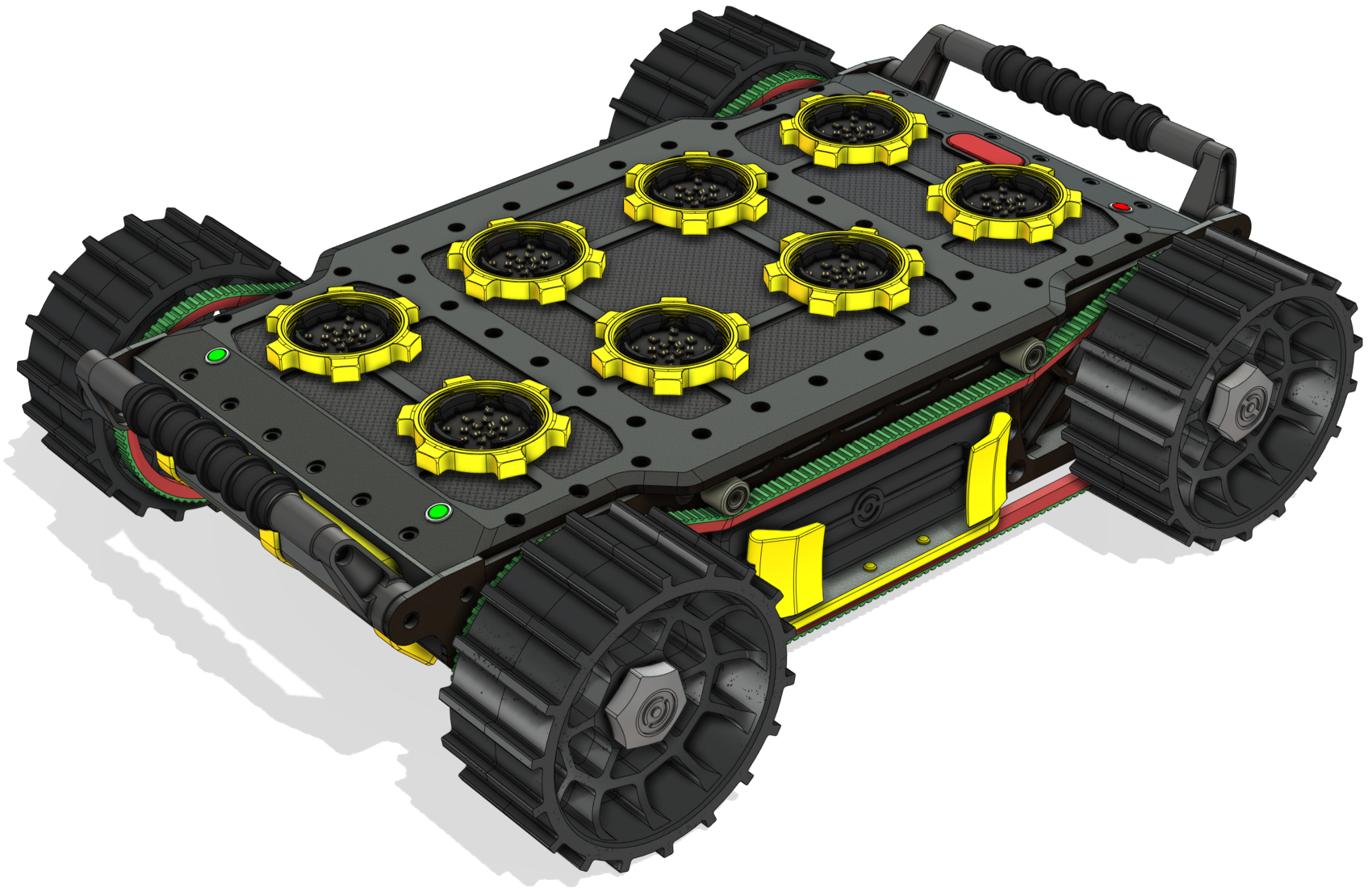
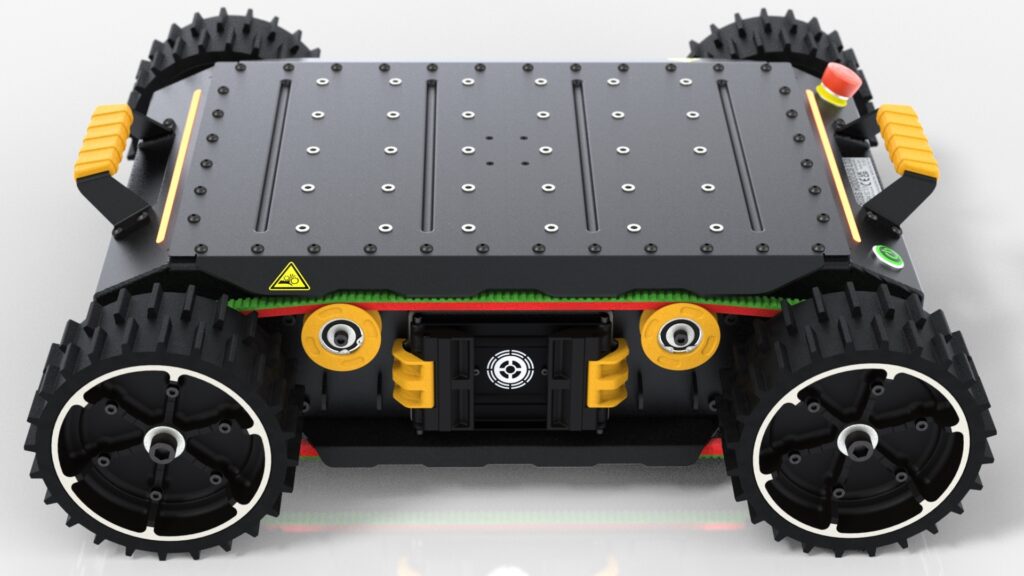
In 2021 I joined Reading-based robotics company Ross Robotics Ltd as a robotics engineer. Keen to combine experience in product development with my hobby of building robots, this was an ideal opportunity. I joined Ross whilst the company was brainstorming a new UGV platform, to replace their existing 3rd-gen systems.
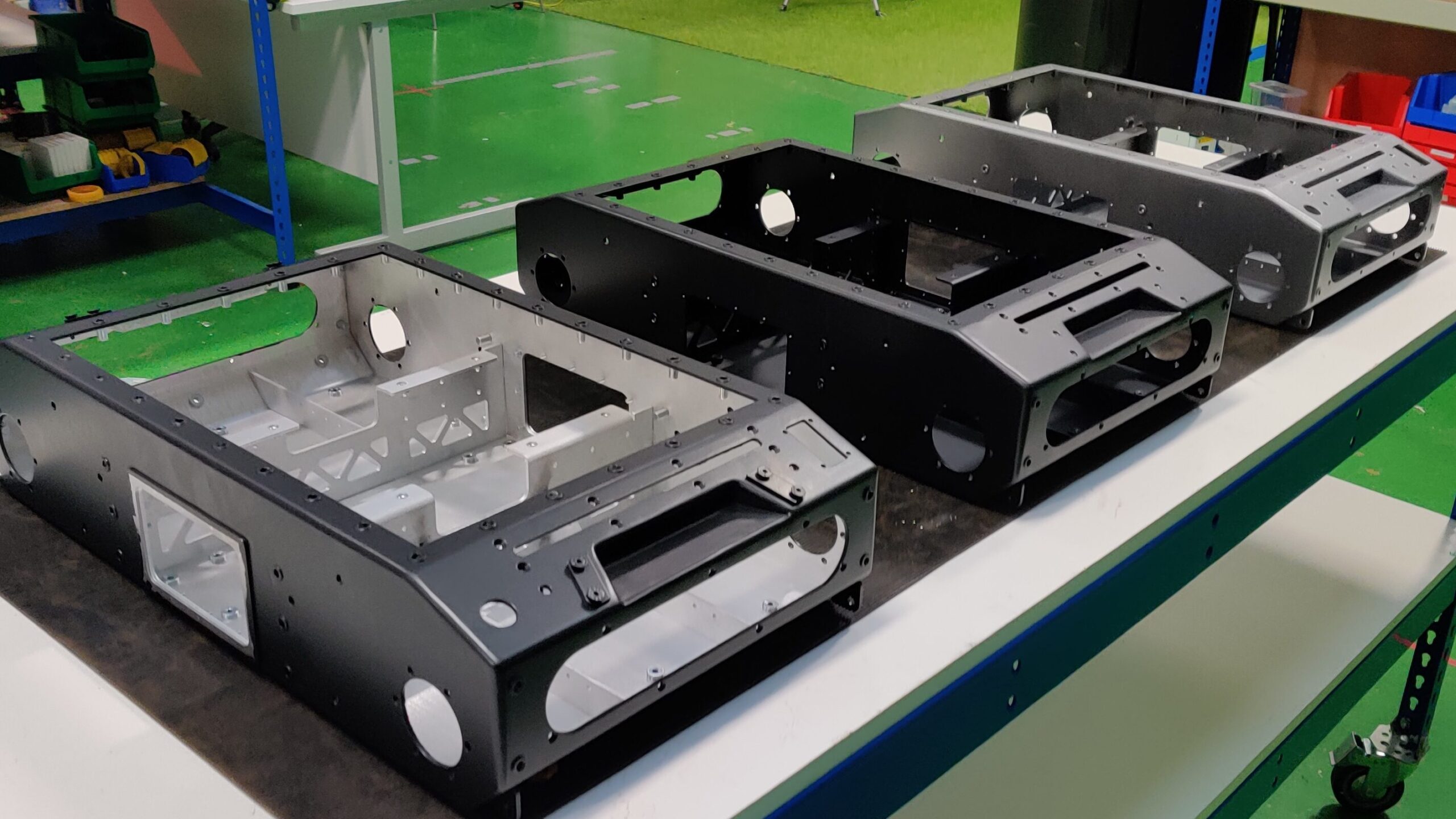
Feet firmly under the desk in a chilly warehouse-workshop, I was soon working on concepts for the “MK4” robot. Simplifying manufacturing, slashing assembly time, correctly approaching modularity and ideally adding some design flair were the headline goals. I was given freedom to crank out rendered SOLIDWORKS visuals for internal and stakeholder meetings, as we raced towards the new generation of robots (a seriously fun process). I led the charge in the mech team, landing on a custom transmission, sheet-metal and welded monocoque chassis, powder-coated finish and tactical design language. The work I did on MK4 is in action today.
– 2021 – 2017 –
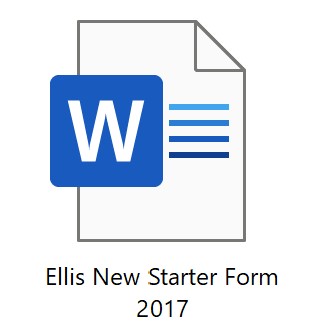
After featuring on all three series of the BBC Robot Wars reboot, I was offered a job at RPDK (then RPD Intl) on the merits of my creations, via Twitter DM from the CEO. A truly 21st century hiring experience. I joined the agency as an electro-mechanical engineer and was their youngest new-starter, having just turned 21. I was very quickly dropped into product development’s (and life’s!) outside lane with a move to central London, complete with a bad house share, meal-deal diet and mid-week drinks.
At RPD I switched back to SOLIDWORKS after a few years with Autodesk Inventor, and encountered new challenges and projects almost daily, at every level of product development. From very first client calls and ideation sessions leading to quoting and budgeting, through the entire design and engineering cycle, including production management, certification, factory time in China, and delivery logistics. The A-Z of bringing a product to market.
I worked on dozens of projects, but two great examples are mojo and SoundBops:
The IVD mojo microscope is a hardware vessel for AI-powered male fertility analysis. I was tasked with taking the client’s very early prototype ideas (recycled 3D printer parts) and turning them into a polished, clinic-ready machine. My role was lead engineer, but also project lead, technical liaison in all directions and production manager. I knew from the very first discussion that whatever shape this thing would take, it would need motors, belts, bearings and all manner of machining. Up my street!
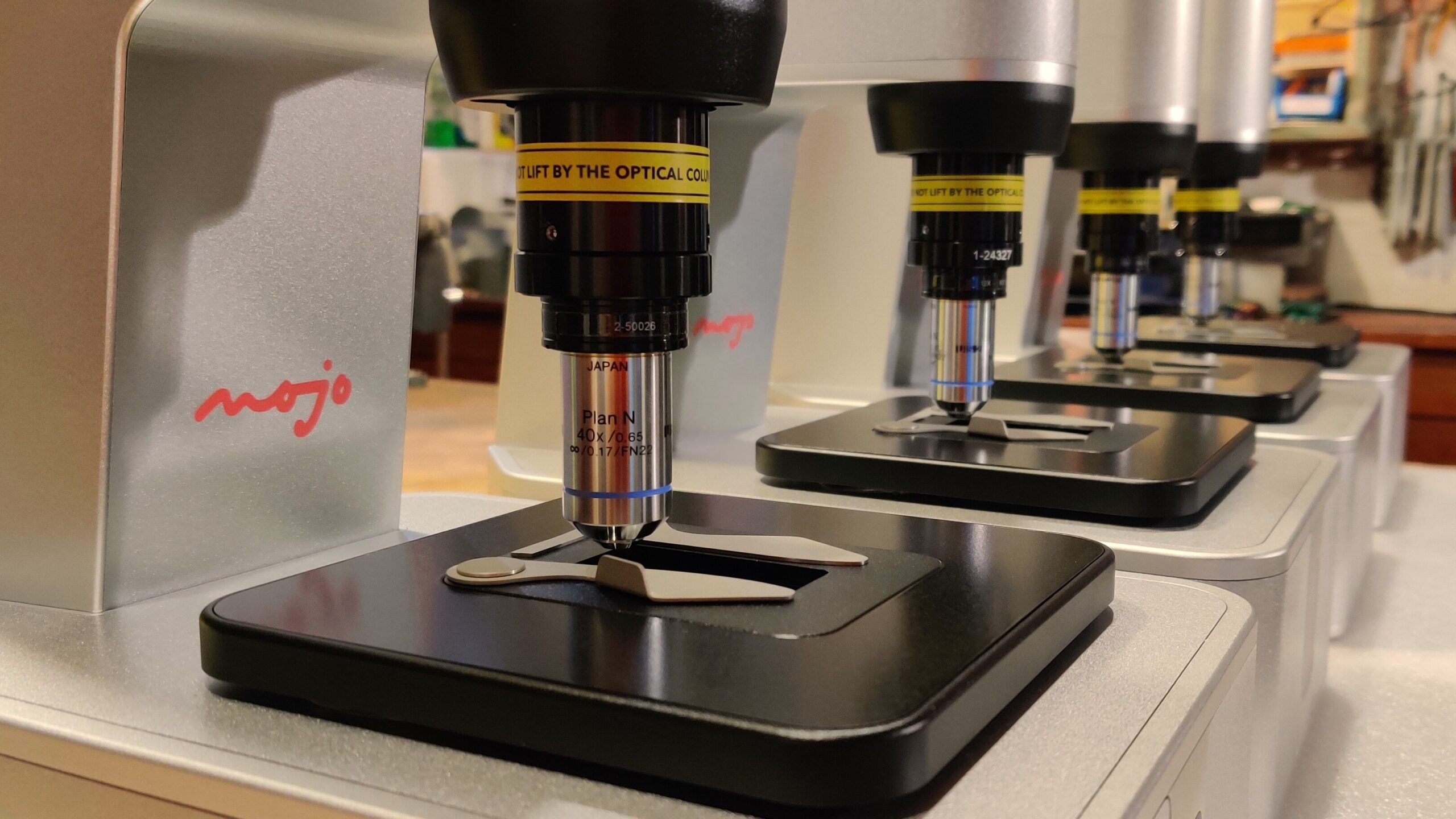
After an extensive documentation phase I ran 3 prototyping rounds, with each one nearing a polished product after many hours buried in SOLIDWORKS. The final machine features 750+ parts, a heated and “floating” sample tray, bespoke condenser optics, custom harnesses and a Z axis resolution of 0.0002mm (not a typo!) achieved with a fun little snail-cam. An anodised and powder-coated CNC structure completes the “if Apple made a microscope” vibe.
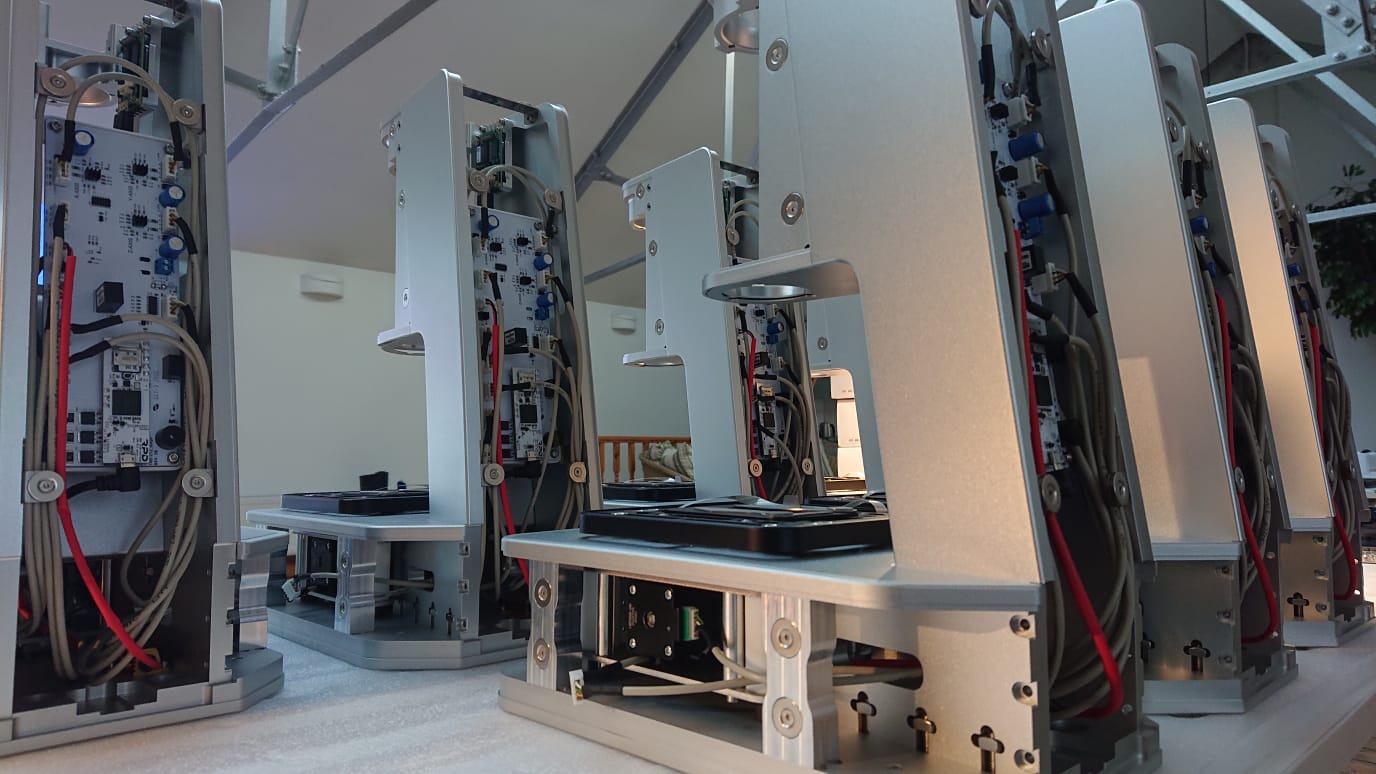
Development and ultimate production ran through COVID-19 just for an extra bit of challenge, but after approximately 2 years from start to finish, what is possibly my proudest commercial project was alive and certified. It took an army of talented engineers and a lot of dedication from all, not just myself, and these microscopes continue to change lives daily.
SoundBops is a novel children’s music toy which exists somewhere in the space between a keyboard and a DJ controller. It features 13 “towers” over which a musically inclined youngster could slide up to 3 “bops”, with each bop pertaining to a specific note. Hit the buttons and the toy will play the corresponding notes in the selected instrument sound. Headphone jack included (for parental sanity).
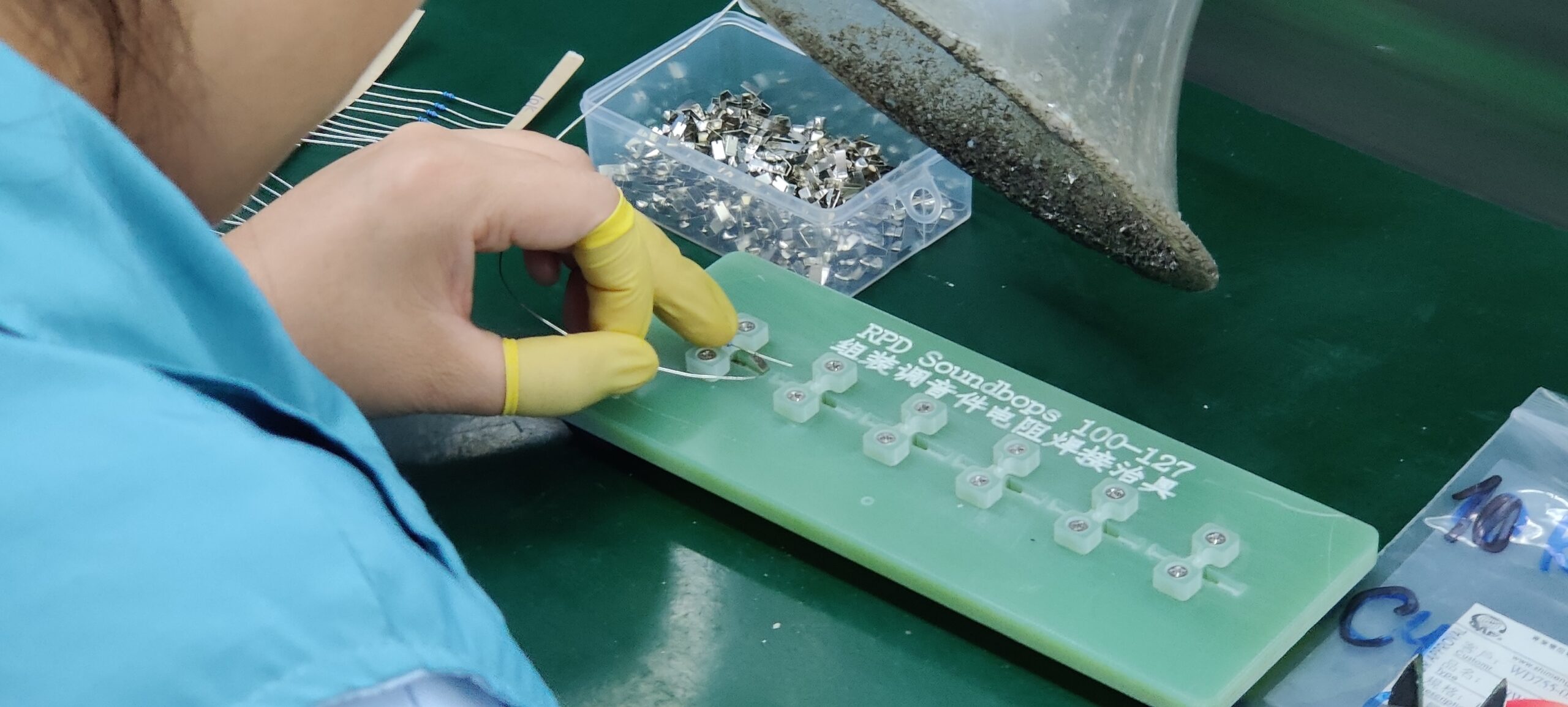
The shape of the toy calls for injection moulding, and I was thrust into that specific world of DFM. I was responsible for the complete mechanical scope, not just the plastic parts, meaning details like the perforated steel and powder-coated speaker grill, the pad-printing and stickers, bespoke beryllium copper contacts in the bops and all of the product’s eventual packaging and leaflets. Several trips to China after multiple design and tooling rounds led to one of the company’s most ambitious injection moulded products bringing joy (or sound, at least) to Christmas mornings around the UK!
– 2014 –
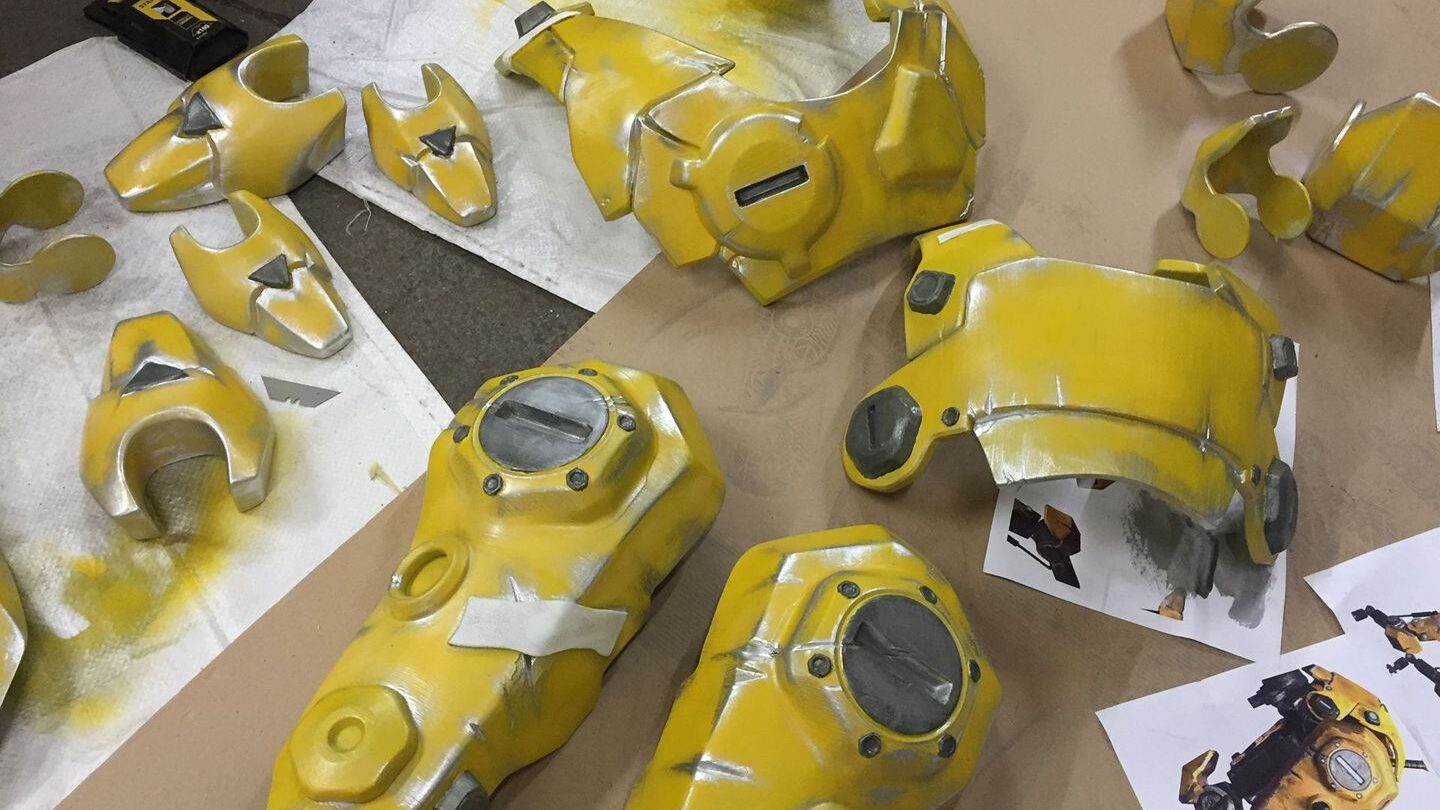
My first “real job” was at Birmingham-based bespoke engineering firm Robo Challenge Ltd. My effort was evenly split between Autodesk Inventor in the office and hands-on workshop time. Think mad sculptures at conventions, bizarre contraptions for TV ads, and the actual house robots from Robot Wars, that kind of thing. I particularly recall spending several days gluing, filling and sanding a full-size replica of “Mack” for Microsoft’s press work.
Late 2014 is also when I originally started Ranglebox, with several early lessons in the ups and downs of getting parts made in China.
Of course, this is just a snapshot of a few projects in a professional career spanning over a decade. Take a look at the hobby or media pages to see what I get up to the rest of the time. 🙂